Are you normal?
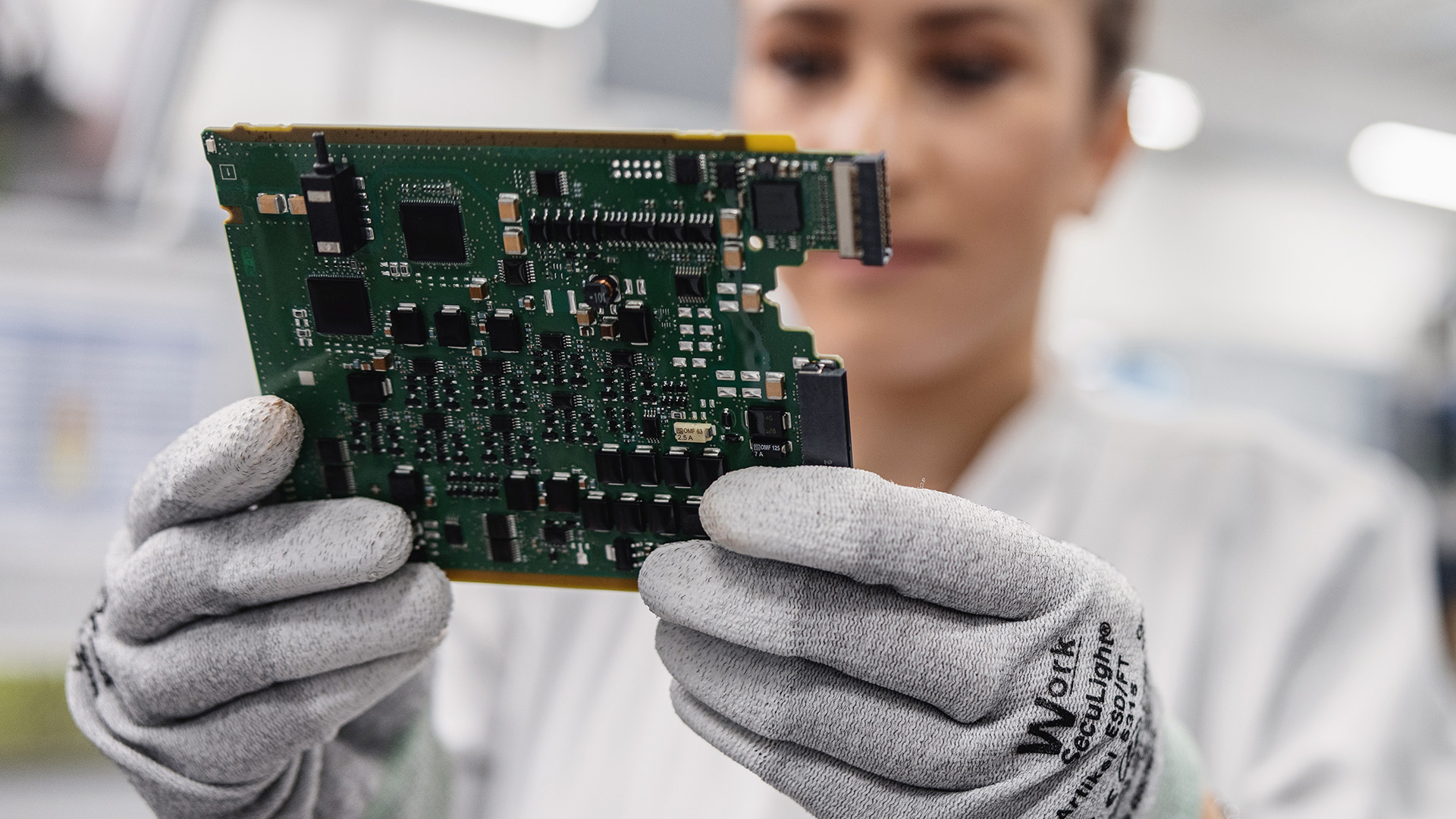
Findings of what is typical for DFM practices in our industry
Siemens recently commissioned a survey through Aberdeen Research looking at the state of the Printed Circuit Board (PCB) industry within North America and Europe to learn about the challenges the PCB industry sees. It covered the technologies they are implementing, the general timelines they are given, and to learn how Design for Manufacturing (DFM) strategies and software are being leveraged to help meet a company’s overall goals. In general, the survey found solid measurable connections between OEM performance and the use of DFM across companies of all sizes and within multiple industries.
The study covered OEM companies divided into 7 key industries: Industrial, Communications, Automotive, Computer Technologies, Consumer Devices, Medical, and Aerospace & Defense. These ranged from small companies of less than 100 employees, to large enterprise companies of more than 5,000 employees. The study examined their individual workflows, technologies deployed and overall product output, and then connected these attributes to the benefits that they receive connected to their DFM processes and software.
Time to Design
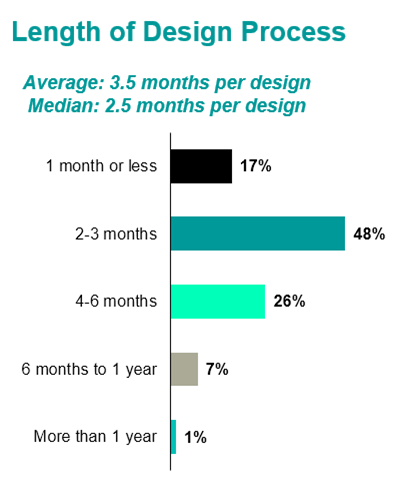
Aside from the direct relation to the deployment of DFM, the results also provide us with a valuable industry overview which showcases the average turn-around time for designs amongst these different companies.
The length of the design process was amazingly evenly distributed. Respondents were asked: “How long does your design process take from completion of schematic to manufacturing release.” In general, regardless of the size of the company, or the industry served, we see an average of about 3 months spent per design. This represents the PCB layout and release process. On its surface, this number feels remarkably short, but it gets confirmed anecdotally when you begin speaking to designers. However, I think you will find that speaking with other PCB designers will indeed confirm these times as realistic industry expectations. Within this schedule, at what point are you making manufacturing trade-off decisions? This aggressive timetable must underline the need for the entire ‘shift left’ movement itself.
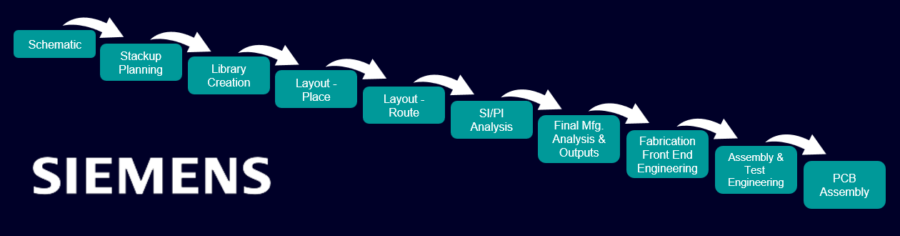
Inarguably, design decisions must be made as early as possible. A great example of this is with our overall material decisions and PCB stackup construction. Where in this schedule do you have your stackup planning? Perhaps for you, as it is for many, it is NOT even on this timetable – it is something that has been pushed off to your fabricators as something they do and sits at a step just prior to sending your design to fabrication. Of course, that’s too late to guide the routing constraints.
Number of Designs per year
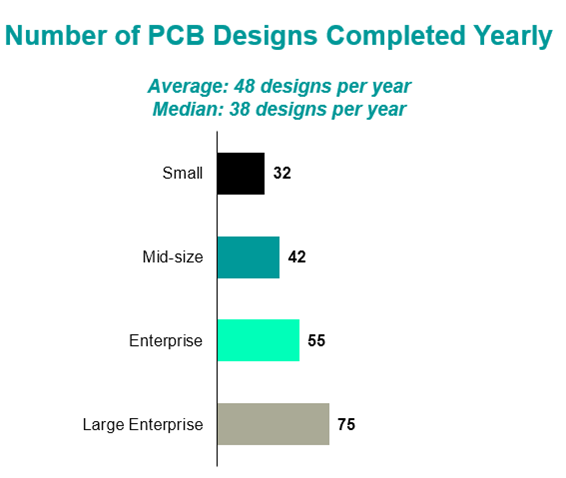
While larger companies obviously produce more designs per year, there are more in-depth and interesting trends at play here. These companies also produce more complicated boards, using more advanced technologies like embedded components, HDI, etc. But independent of the size of the company, the complexity of the design, or the industry served, the biggest factor relevant to the number of designs produced per year was the presence of DFM software.
This is one of the strong indicators and take-aways from the study itself – for these best-in-class companies, robust DFM practices are an important component to help the overall design cycle – by looking within the study itself, the take-away seems clear: DFM helps with the requirements that concern PCB designers and OEMs, with designers listing DFM as important for ensuring design reliability and decreasing the cost of production as the two main take-aways.
DFM becomes an important component when realizing the success of a PCB Design and its use it critical in deploying successful PCB design best practices.
Conclusion
The report ‘Design for manufacturing is a PCB design best practice’ is a summary of the “PCB Design Best Practices in 2023” study performed by Aberdeen group summarizing the state of the industry and DFM in general for 2023. It provides an objective look at the advantages of deploying DFM within a PCB design flow and provides results showing that these projects are more likely to be completed on-time, on-quality and on-budget. In fact, the used of DFM software is the single largest differentiator for best-in-class companies and allows smaller and medium sized businesses to compete with larger enterprise companies.
Within the DFM successes shown by Aberdeen’s study, there is also a somewhat surprising result that shows despite the proven results, DFM software is still deployed by less than half of the recipients surveyed. This represents a significant untapped growth potential for the majority of OEMs worldwide[PM5] . So, are you normal? Have you realized DFM into your workflow? Are you leveraging your manufacturer’s knowledge to improve your product?
Download a copy of the report here to get a more in-depth look at the industry.
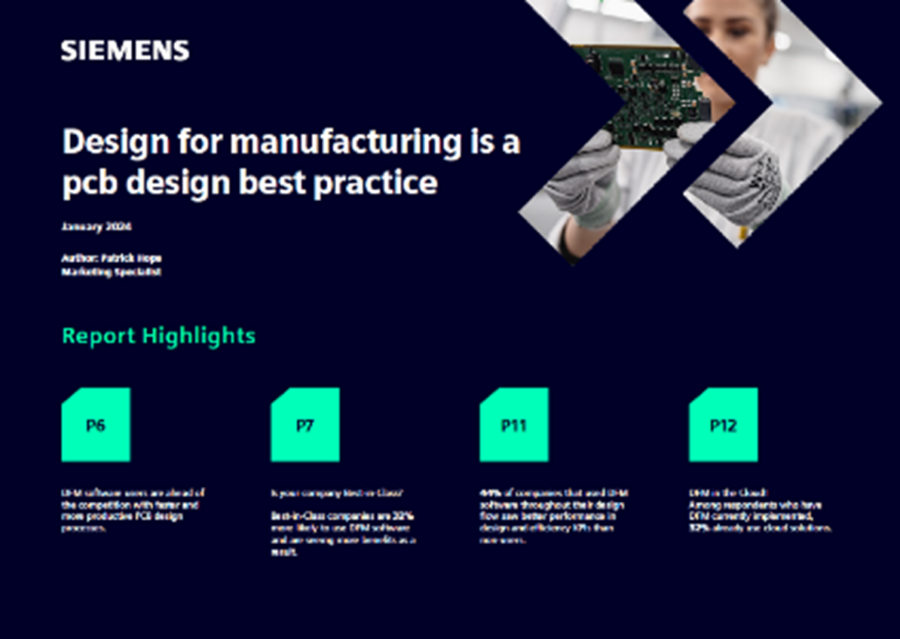