Why develop a comprehensive digital twin?
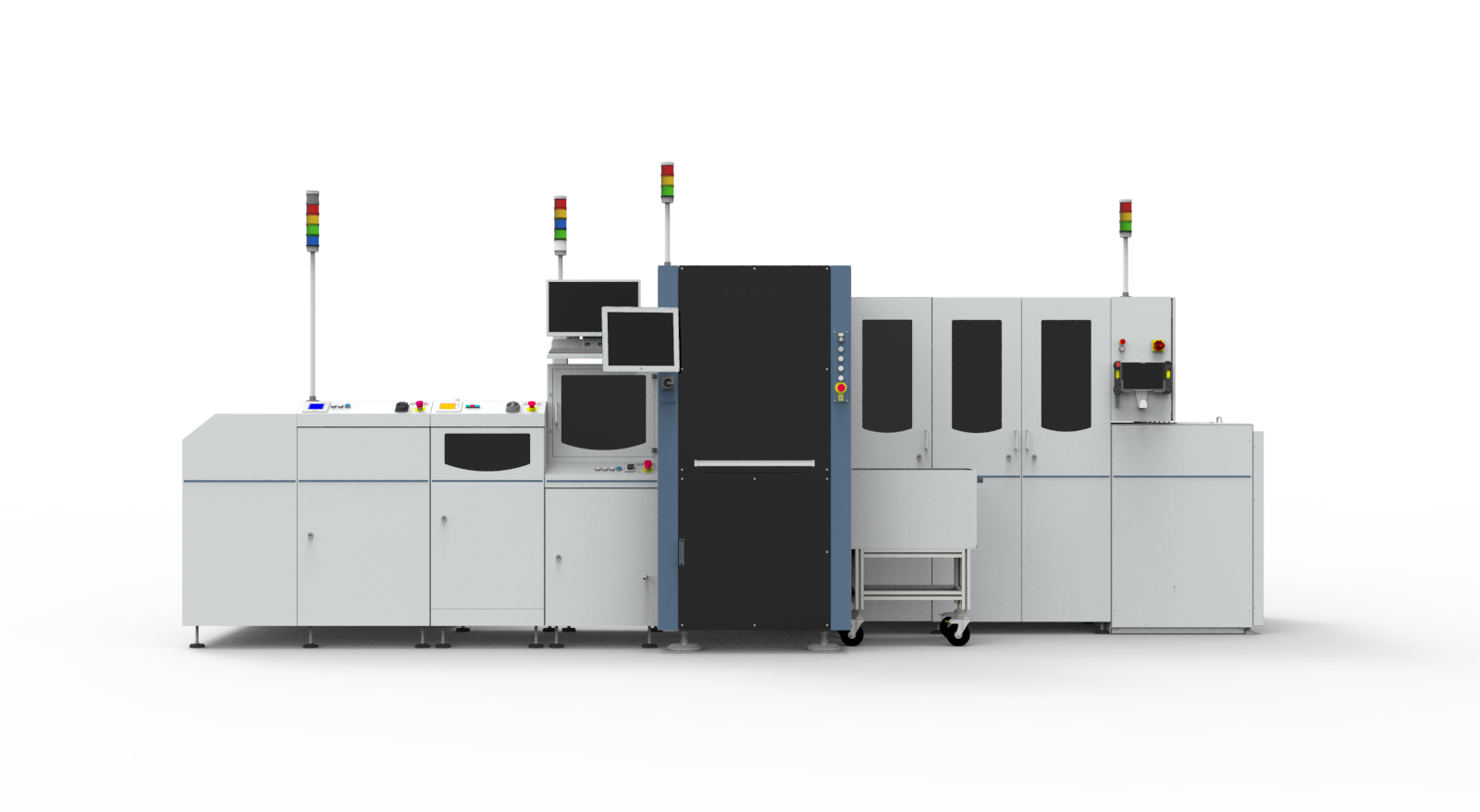
Learn how full virtualization of PCB assembly, inspection and testing can boost manufacturing agility, cost-effectiveness and time to market – explained in our new whitepaper
It’s not exactly news that electronics manufacturing success depends in large part on the ability to respond quickly to product changes, while maintaining high quality and preserving margins. What manufacturer doesn’t already know that!
But, with industry trends such as smaller lot sizes, tighter electronic-mechanical integration requirements, and supply chain disruptions that compel production to move from region to region, the profitability of PCB manufacturing projects is under dire threat. Facing such pressures, it’s vital to eliminate silo-based inefficiencies and errors.
As intimidating as that might sound, there is a practical approach already available: implementing a comprehensive digital twin.
As a virtual model of both the product and production process, a digital twin allows processes to be simulated and corrected before they are implemented on the shop floor. This makes it much more likely that the first batch will exactly right. Ultimately, developing and using a comprehensive digital twin saves time and money and enables manufacturers to meet time-to-market demands.
With this methodology, a holistic product lifecycle management (PLM) tool works with a single, unified data backbone to manage the entire manufacturing workflow. It provides a comprehensive view of the entire process while ensuring subsystems are synchronized.
The mechanical and electronic designs are verified and submitted for manufacturing planning. The individual processes are then derived, simulated and validated. At each step, errors can be identified, enabling corrections to be made to the design. This shift-left on PCB troubleshooting allows problems to be quickly and inexpensively resolved. At the end of the holistic planning process, a virtually error-free execution work plan is generated for use on the shop floor.
Our new whitepaper explains how by providing access to fully synchronized data across the enterprise, a comprehensive digital twin reduces errors on the production line, improving production yields and profitability. It introduces the Siemens approach, implemented through Teamcenter® software and describes how one electronics and design house was able to dramatically reduce its repair rate and all-but eliminate scrap.