What do supply chain challenges mean for intralogistics?
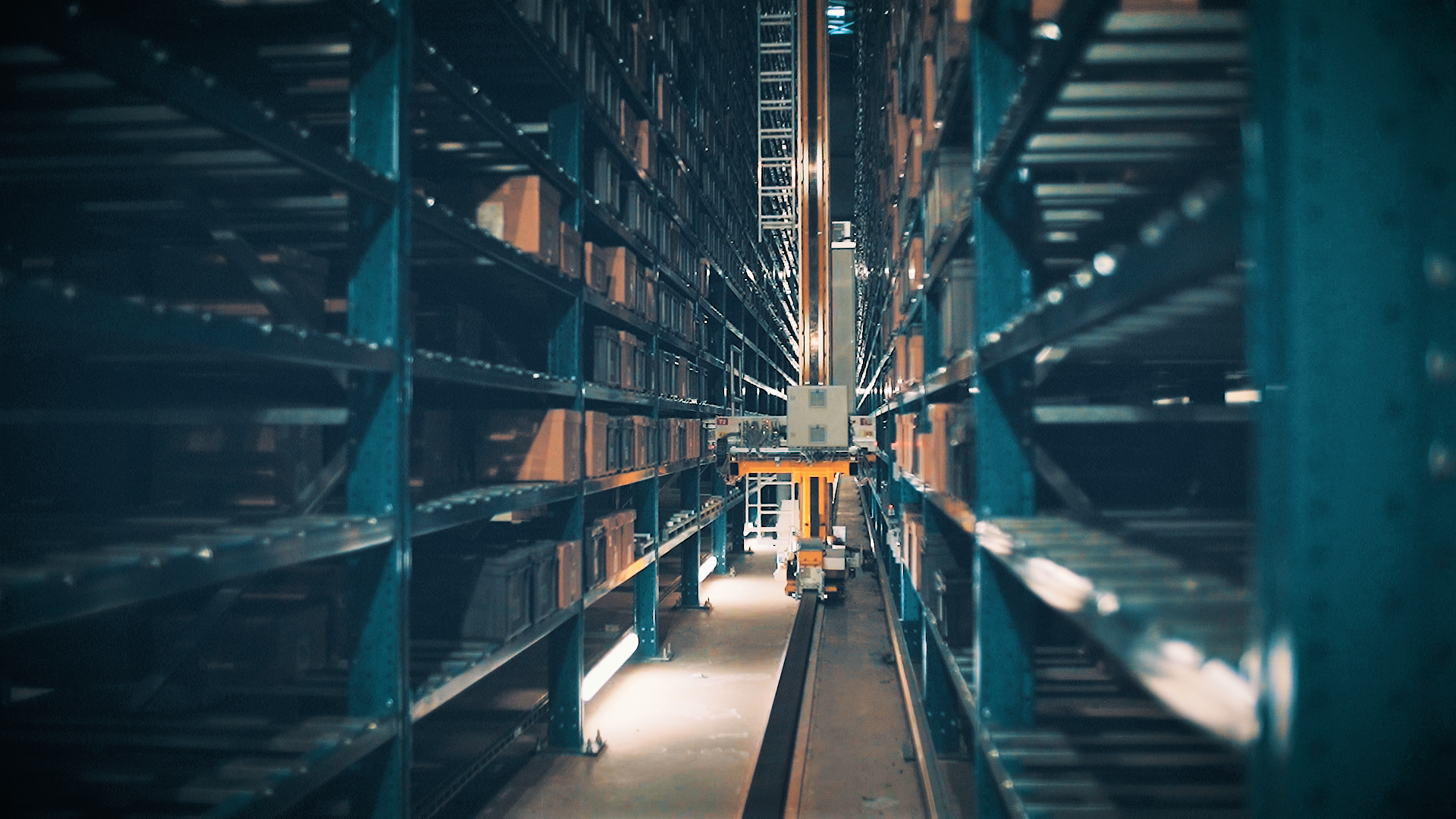
And how is it affecting electronics manufacturing?
Manufacturing challenges have shifted in recent years. In the past, warehouse inventory was usually not a significant source of concern. Components could be sourced easily, and managers were more worried about preventing material starvation on the line. Therefore, the focus was on just-in-time (JIT) delivery—how to get inventory to the production floor efficiently and how to get the right component where it was needed when it was needed. This capacity was critical, especially for lot size one production where manufacturers had to transition from one variation to another as quickly and efficiently as possible.
Today, the newsworthy global supply chain problems have turned the picture on its head. Customers are struggling to source components and in many cases, it is no longer possible to source components for a full lot at once. Manufacturers are forced to be responsive to component availability, producing partial lots whenever they can source the components and conducting frequent changeovers between products. Visibility of materials and smoother, faster material changeovers have become essential in order to manage the shortages and best utilize the available components.
How the component shortage is impacting our customers in the field
Siemens expert Gabor Soos recently visited the production site of a large European tier-1 automotive manufacturer supplier where the challenges caused by component shortages were very apparent. Although it is a large facility, planning and scheduling are still conducted manually on Excel. While logistics orders are received in SAP, they have to be compared to the available material manually. The process is cumbersome and time-consuming.
In the past, that was less of a concern since the facility production plan was built on a weekly basis. However, given current material shortages and long shipping times, products are finished and shipped in phases and the planning team is now forced to adjust the plan on a daily basis based on material and resource availability. The facility planner is constantly calculating how to best distribute the available material for multiple orders and produce at least part of each original order to keep the customers satisfied until additional components can be sourced. Yet using manual processes, it is nearly impossible to stay on top of all the changes.
In addition, when there are a lot of unfinished products on the production floor, many of the magazines are occupied with PCBs. It is difficult to find available magazines for new work orders due to poor visibility of work in progress (WIP).
Challenges like those faced by our client can be addressed with advanced solutions like Opcenter Intra-Plant Logistics. Opcenter IPL helps facilities like this one automate and optimize material management within the facility and gives them the flexibility to manage changeovers easily.
Better management for component shortage challenges
Let’s look at the example of automated guided vehicles (AGV). Unlike human workers, these machines have the capacity to work 24/7, providing a significant advantage to manufacturers. They are also more sterile than human workers, which can be critical for some applications. AGVs can work with pick lists and communicate with shelves to retrieve the items they need.
Machines like AGVs can be better optimized when they are connected to the manufacturer’s MES. For example, when systems are integrated, AGVs gain the capacity to automatically respond to changes like material shortages in real time. Intra-logistics systems like Opcenter IPL can tell an AGV exactly what is available, where it is, what can stay on the floor, and what is not needed and can go back to the warehouse in real time without any human involvement. Manufacturers gain the visibility and flexibility they need to make the most of their available components.
Summing it up
According to U.S. Commerce Secretary Gina Raimondo, the global shortage of semiconductors is likely to last at least through the end of 2023 or even longer. That leaves manufacturers with no choice but to find ways to manage them effectively in order to remain competitive. Intra-plant logistics solutions like Opcenter IPL can play a key role in solving this complex puzzle.