Teamwork and creativity for sustainable manufacturing
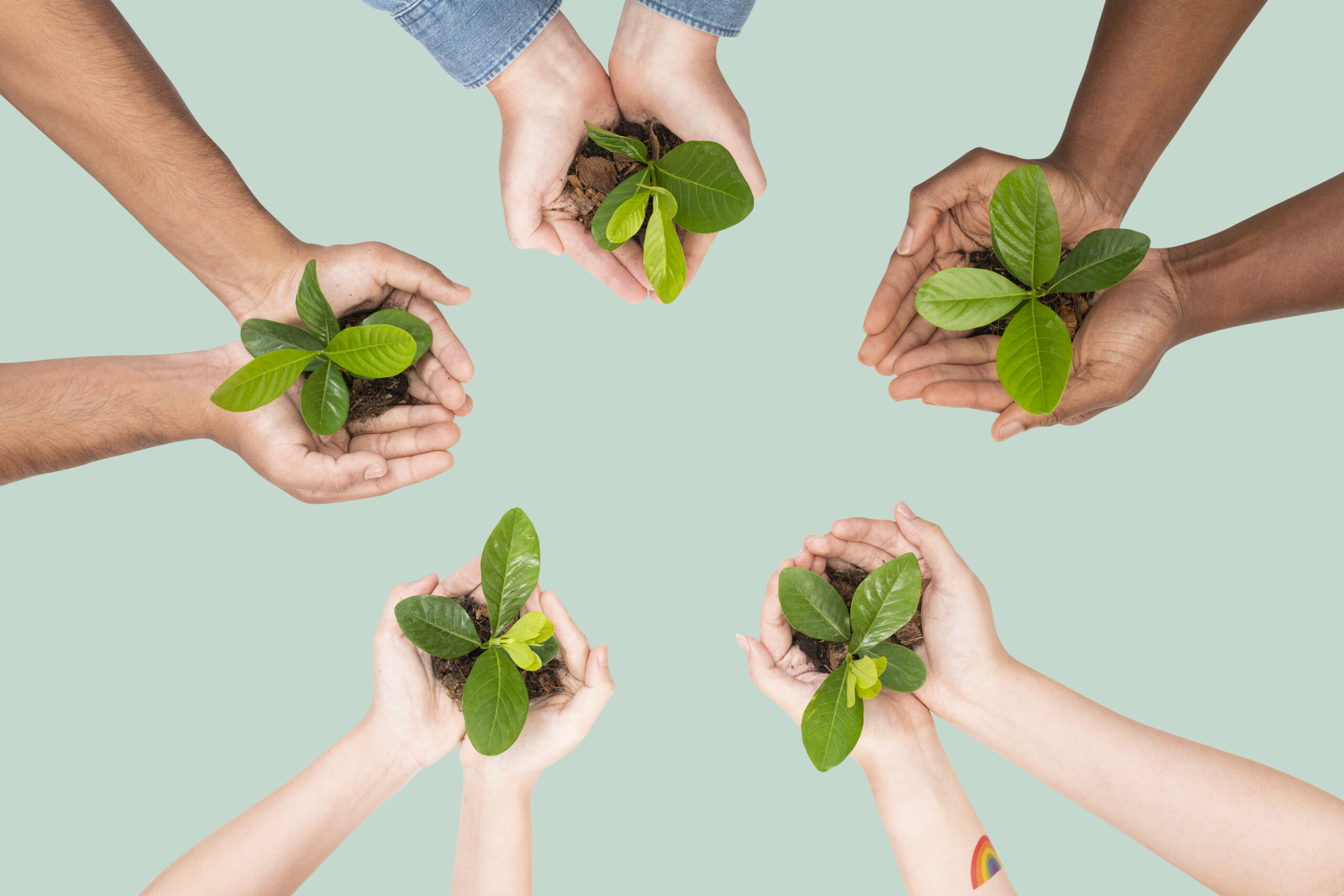
Podcast #6 in our new series with I-Connect007: Sustainability in Electronics Manufacturing
Creating a more sustainable manufacturing environment is essential for the future of our planet. It is not just the responsibility of one department or one person, but rather a team effort involving all stakeholders. In order to achieve this, we need to think creatively and approach resource efficiency holistically.
One major aspect of doing things differently is involving all stakeholders in working on solutions. This means that we need to have data to have a meaningful discussion and decide on specific KPIs. For example, if we want to answer the question of whether the bottom line is better when shifting production to when electricity is green and has a zero or even negative price, we need to assess the energy cost, overtime, risk of issues, and whether we have the right software to handle new schedules. Even if the answer is currently no, we can identify gaps that will make it viable and improve our processes through continuous improvement.
Organizations don’t usually spontaneously start collaborating on holistic projects, so two important success factors are leadership agenda and defining an internal champion who will help steer the ship towards the environmental target while considering all other stakeholders’ targets.
Being more systematically creative
Creativity is also essential to more sustainable manufacturing. But being creative might not come naturally to everyone; this is where the 7 R’s for sustainability help us, by providing a systematic approach to finding new solutions:
Rethink, Reduce, Replan, Reuse, Reject, Recycle, Renewables
Listen to the full podcast with Jonathan Fromm to learn more about these tools and how they fit in with the manufacturing environment.
It all needs to be measured
Once KPIs have been discussed and defined, analytic tools can help monitor and provide alerts when specified thresholds have been crossed.
OEE is one such useful KPI: tracking OEE levels allows manufacturers to find areas of low productivity, utilization, and quality and by improving them it can have a positive impact on the energy efficiency. For example, a reflow oven energy consumption would not change much, irrespective of the quality of the product, however with a higher FPY there would be a lower energy consumption per unit shipped.
Similarly if the line utilization drops, additional overheads including energy consumption (for example air conditioning) are still being consumed, particularly if other lines are still producing.
Component analysis can also help improve sustainability KPIs:
- Some suppliers provide better quality components than others. Manufacturers need to be able to identify which suppliers’ components perform best, so that they can minimize quality issues as a result of compromised components. Monitoring materials from the moment it enters the factory until it is placed on a PCB helps to identify issues with specific reels or suppliers during quality testing.
- Not using components in time can also create waste – without monitoring closely component expiration dates, manufacturers risk wasting large amounts of components that should have been used earlier. Analytics tools provides constant monitoring and management of the inventory, allowing manufacturers to ensure that components are used in time.
For more insights, listen to the full podcast with Jonathan Fromm.
Previous podcasts in the series
Listen to the full series!