Coronavirus Impacts on the Electronics Industry: Playing “Hot Potato” in Manufacturing
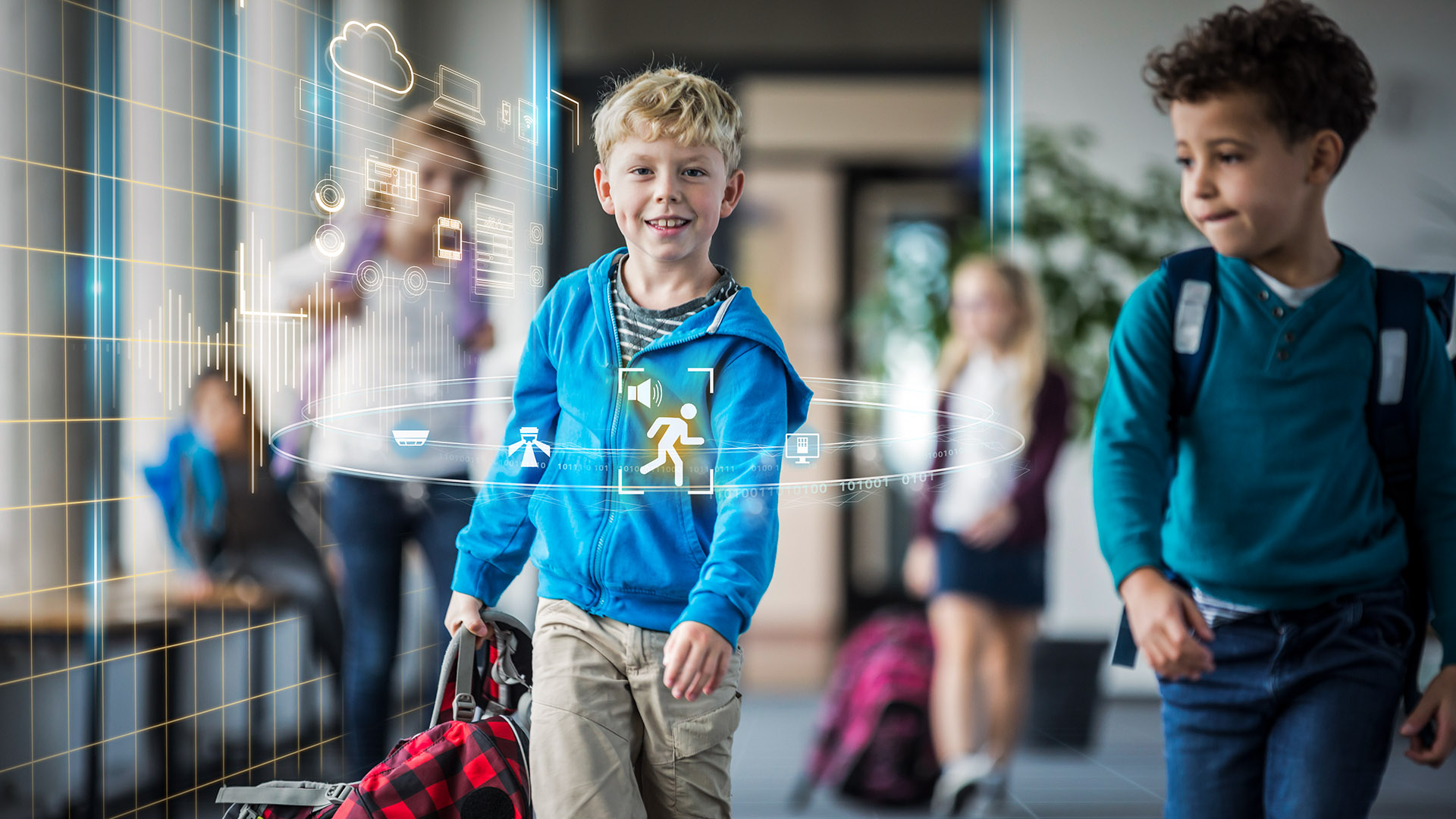
In the children’s game of Hot Potato, a “hot potato” is passed from one person to another, until the music randomly stops. The person holding the potato is “out.” It seems manufacturing is dealing with a similar game. Manufacturers have to pass capabilities, products and manage supply chains in order to stay ahead of the impending “music stop.” The music, in this case, includes geopolitical disruptions, climate disruptions, economic disruptions, and most recently, a global pandemic.
What started with the U.S.-China tariff battle that reached a boiling point last year to the onset of the COVID-19 pandemic, disruptions seem to be more prevalent than ever before. Under the new reality, the world’s electronics OEMs and manufacturers are actively seeking ways to diversify their supply chains and have the flexibility to decide where to build to manage costs and quality.
As I mentioned in my Blog Enter the decade of “Smart the Gathering,” we will see design to manufacturing and integrated manufacturing planning for the whole product. Software, mechanical, electronics, and electrical systems design need to be planned as a whole. This also should be done such that manufacturing planning for all parts of a product is done in an integrated manner, each with related domain-specific and industry-specific capabilities and functionality. However, manufacturing planning at the product level is not enough. It must also consider manufacturing and process planning based on plants’ assets and processes at various locations. To achieve this, manufacturing and process planning capabilities must be characterized in a solution that can then define Manufacturing BOMs, based on the Engineered BOM, and establish a process and plant Bill of Process (BOP), unique to the plants located around the world. Only then can global flexibility be achieved.
Read our white paper: Portability is Key to Success for PCB manufacturers>>
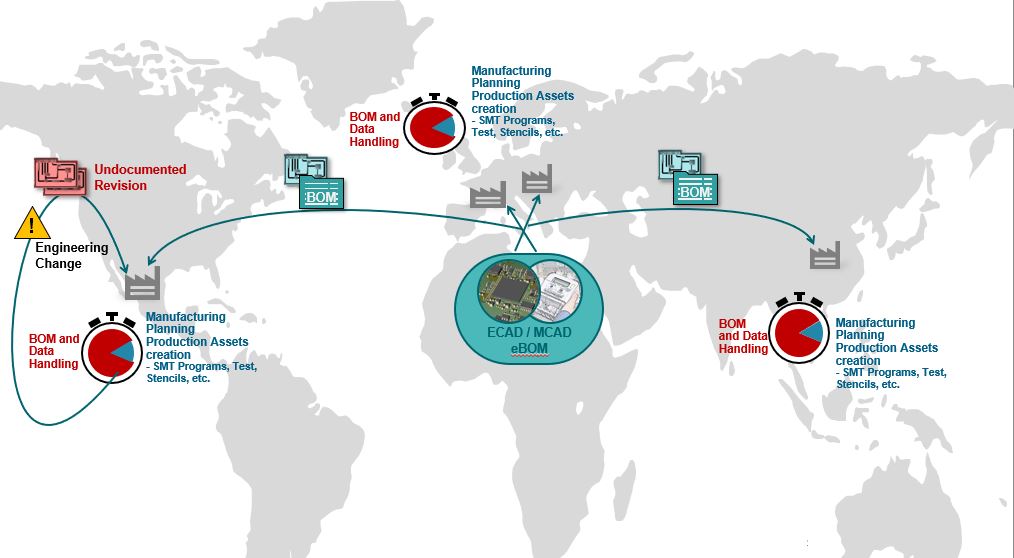
PCB assembly manufacturers need flexibility
It is times like these when manufacturers need the most flexibility. It may be due to COVID-19 or geopolitical shifts that affect workforce availability, cost structures or changing supply chains. However, PCB Assembly manufacturers that have multiple plants typically allow each plant to perform manufacturing planning, process planning and develop the BOP for their individual plants. The data handling is repeated for each plant. This makes it almost impossible to manage engineering changes (ECs), product change notifications (PCNs), and revision changes driven by the customer and/or the originating plant. Moreover, there may be different BOPs leading to variances in Production from one plant to another for the same product.
A “single source of truth” in an integrated manufacturing planning solution, which is synchronized with design data and engineering changes, is required. When there is a common enterprise data management layer across plants integrated with process and plant models, then true flexibility can be achieved.
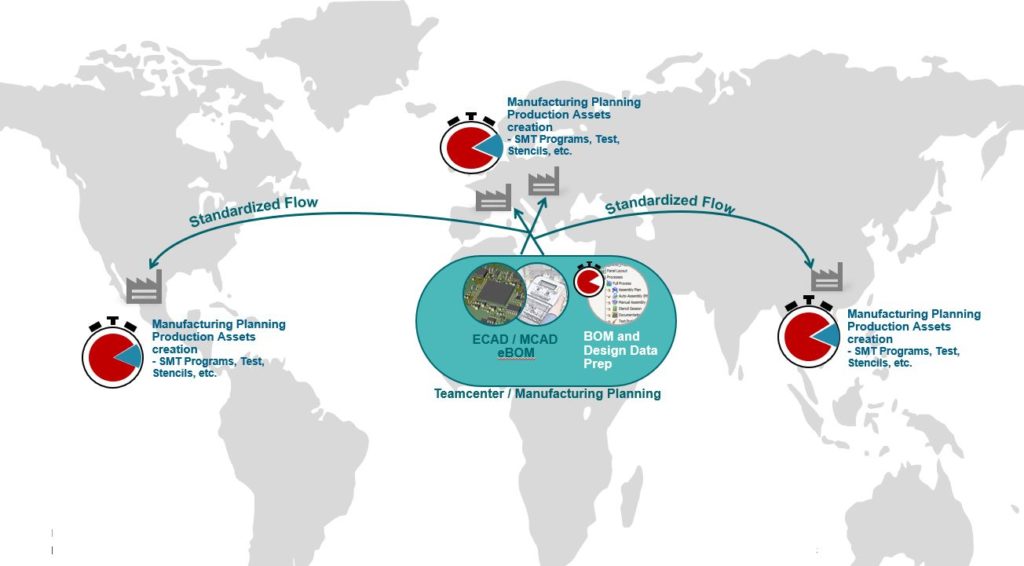
These are unprecedented times. A Gartner, Inc. survey of 317 CFOs and Finance leaders on March 30, 2020 revealed that 74% intend to move at least 5% of their previously on-site workforce to permanently remote positions post-COVID 19. The more manufacturers leverage software solutions designed to optimize efficiencies across borders, remotely, safely, only then can manufacturers have the flexibility to move Production where needed, with the best outcome.
For more information on PCB production portability, read our white paper: Portability is Key to Success for PCB Manufacturers.
Comments