New infrastructure: the only way to improve shop floor productivity?
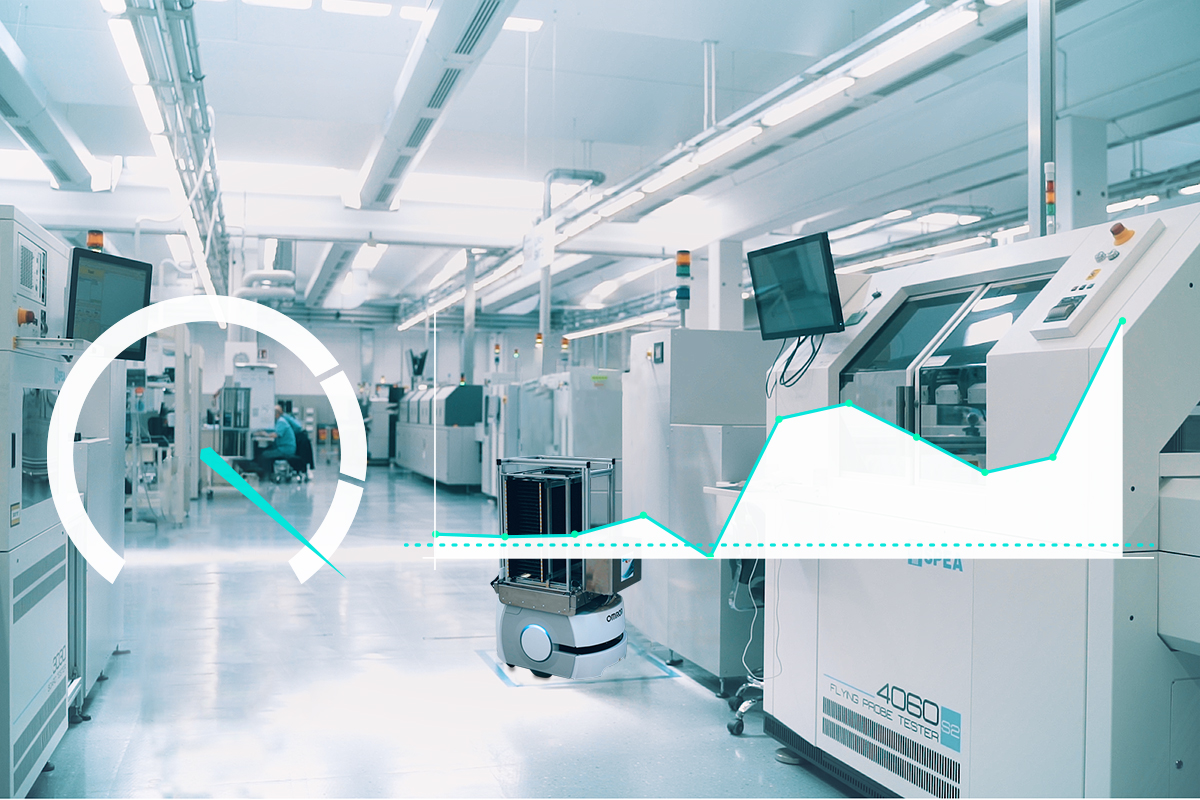
Find out in our new white paper on improving the SMT process.
Electronics manufacturers looking to improve operational productivity and yield in their SMT assembly process often believe that their only option is investing in new infrastructure. Confident that their efficiency levels are already maximized with their existing equipment, they think the only option is to update it.
That’s not always the case. We’ve put together a whitepaper that presents four proven methods for improving your bottom line by raising line and machine utilization levels without investment in costly SMT assembly line machinery. The methods include:
Accurately assessing your current level of efficiency
It’s hard to decide whether or not to invest in new equipment for your SMT assembly process if you aren’t sure about your current OEE—the manually collected data traditionally used to calculate OEE was not always accurate. Data collected and calculated using automated shop floor collection techniques can deliver better results and new contextual interpretations that can help you understand where problems exist and what needs to be improved.
Using a scheduler to improve resource utilization
An automated scheduling generator can significantly improve utilization of shop floor resources without investing in costly new SMT assembly equipment. By creating optimized manufacturing plans based on customer orders and production constraints like line capacity, personnel availability and control critical parameters, an automated scheduling generator can help you optimize performance by comparing multiple what-if scenarios and making on-the-fly adjustments.
Implementing JIT methodologies
Another way to ensure that the correct quantity and quality of materials are always delivered right on time, without pre-kitting, is using an automated bill-of-materials (BOM)-aware system that receives “pull” signals from machines that can access work orders from the ERP system. An automated digital management system also prevents SMT machines or processes from working until all of the materials have been correctly set up as defined in the work order.
Reducing changeover times
One of the simplest and most effective ways to improve productivity is to reduce changeover times on the SMT assembly line, for example using automated materials management software like Valor™ Material Management software. The Valor solution, which helps improve operator and SMT assembly line efficiency, includes a changeover guidance feature, which enables continued use of the material currently mounted on the machines for the next work order.
The whitepaper explains these methods and more and is a must-read for manufacturers who are considering purchasing additional machinery in order to improve production yields.