The key to successful and cost-saving inventory management
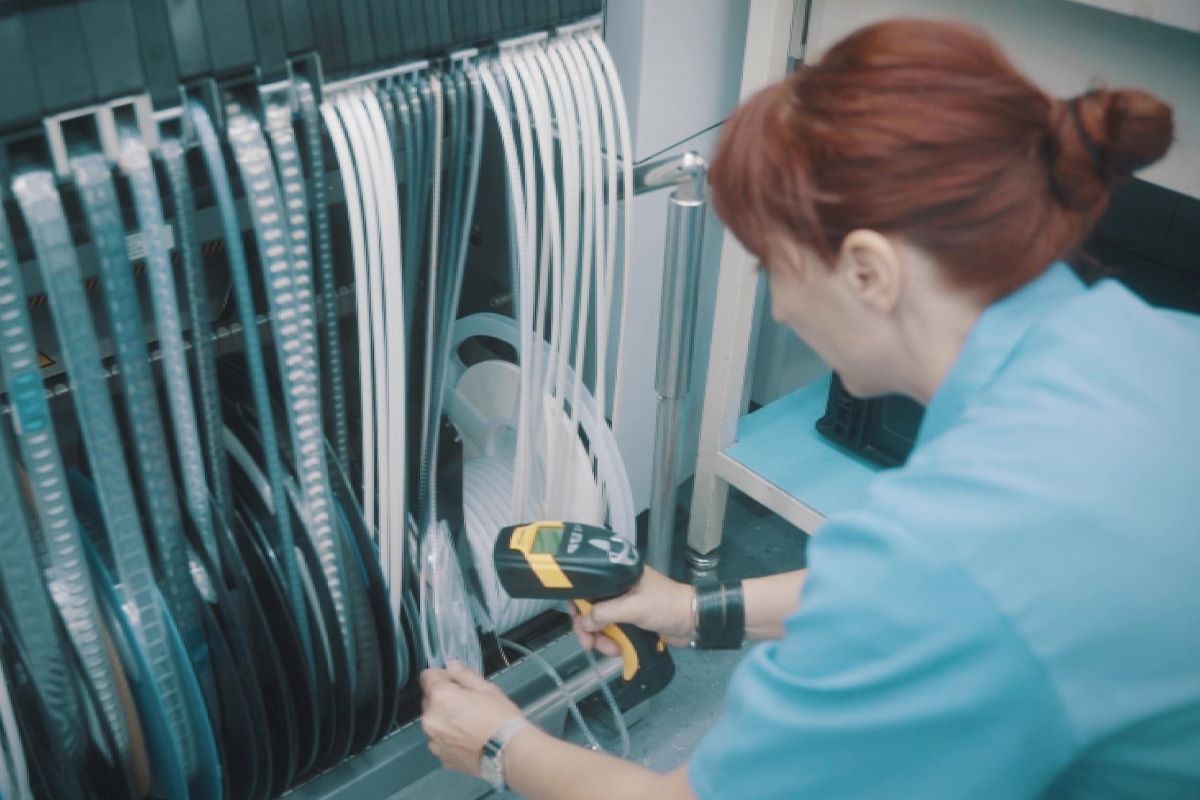
Blog #10 in a 12-part series covering the Digital Twin Best Practices in Electronics Manufacturing mini-webinar series by Jay Gorajia
We’ve all seen how inefficient materials management can affect electronic manufacturing operations and bottom-line results: A single missing component can cause downtime on the production line, as well as project and delivery delays, and a damaged reputation.
In order to prevent such a costly occurrence, manufacturers often over-compensate, taking a series of preventative actions:
- Ordering “buffer” stock, and keeping a bloated materials inventory in the warehouse, often leading to spoilage.
- Preparing kits well in advance – sometimes up to 48 hours beforehand – thus making production plan changes more difficult.
- Moving more inventory to the shop floor, crowding the production area, and causing a growth in the quantity of untracked work-in-progress materials.
As time goes on and the gap between ERP inventory levels and actual physical stock grows, a physical inventory count becomes necessary, putting a halt to regular operations, and wasting precious time and manpower resources.
When analyzing the root cause of materials management failures, we often discover that the lack of visibility of materials currently on the shop floor is a major issue. How can ERP systems be updated to account for materials that are no longer in the warehouse, but still not used?
In the tenth session of our series of 12 mini-webinars on Implementing “Digital Twin” Best Practices From Design Through Manufacturing, we take a look at the materials management challenges currently facing manufacturers. We then review a number of methodologies that can be used to maintain inventory accuracy, track the location of unused materials, and keep materials-related losses to a minimum.
Main takeaways from this session:
- The centrality of successful materials management in achieving profitability in electronics manufacturing operations.
- How Valor® Material Management helps manufacturers meet inventory management challenges, reducing cost, enhancing efficiency, and improving product quality.
- How the ODB++ Manufacturing protocol and its standardized language helps improve inventory control and reporting processes.