Safety Lifecycle Evaluation Part 2: The Data is Compelling
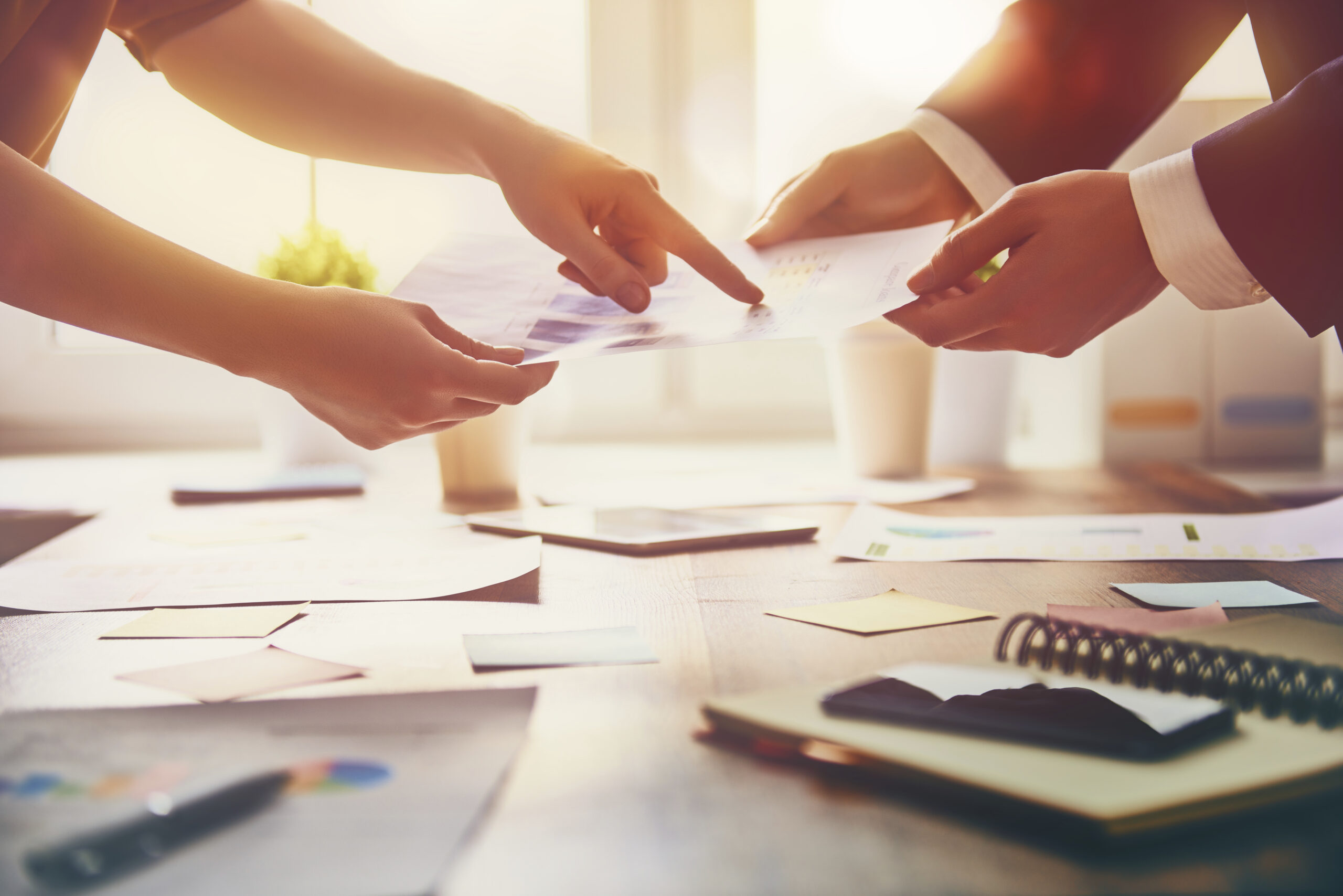
Introduction
This post builds upon the first post titled Key findings of a safety critical lifecycle evaluation. Simply put, productivity is in the details. The consulting firm’s 2-month Safety Lifecycle Study revealed significant insights that impact productivity, and this post dives one level deeper into the findings and data supporting those findings.
Identified Productivity Gaps
Maintaining many small software solutions from a large array of vendors is not efficient. One well integrated system or system of systems is a better alternative. Many companies have a legacy of software solutions that are not integrated, so data cannot easily be shared. And even when numerous software solutions are integrated, maintaining so many integrations is not scalable. Or efficient. And maintenance can be a beast.
Less is more. The industrial components company in the study had attempted to integrate nearly 200 solutions and benefited from reducing that number by 32%, through replacing the hodgepodge of smaller solutions with a single lifecycle solution.

Compliance requirements and verification add an exponential layer of complexity. Incorporating all requirements, compliance and verification data in one system is a better option. The company in the study was managing compliance requirements and verifications on spreadsheets, with zero traceability. They had many compliance standards and requirements they had to track. Traceability is critically important for audits and compliance verification, so access to proper linkage for the sake of audits is a must. Lifecycle solutions must have full end-to-end traceability.
Managing a large collection of variants created by many business units and teams is difficult to manage, to trace and to report. Modeling, libraries (or collections), and governance of variants make it easier to manage variants. The industrial components company in the study produced thousands of differentiated product variations across major product groups. Voice of the Customer requirements created many dependencies that need to be linked and checked. No one system incorporated or managed the requirements. In dealing with complex applications, variant management and reuse capabilities provide exceptional value.

Governance and project management over requirements and verification is hard to manage across segmented team and siloed systems. Maintaining governance in a system or system of systems improves project delivery times and quality. Requirements, quality, test and project management that are managed across multiple solutions present unnecessary risks and are typically not well governed. This opens the door for defects, rework, and delays that impact revenue. Lifecycle solutions provide many capabilities that make governance easier. And the positive impact that improved product quality and delivery times have on the customer experience can make a real difference.

How success was measured
The consulting firm’s 2-month Safety Lifecycle Study helped the company to assess the value of a proposed integrated lifecycle solution. Productivity was measured with value and non-value add tasks, verification effectiveness, solutions used, and time to complete a collection of tasks. The Safety Lifecycle Study looked at how productivity would improve with an integrated lifecycle solution. The consultant compared productivity with the 200 legacy solutions vs. the integrated lifecycle solution, to correctly gauge the positive impact a new solution would have.
Conclusion from the study
The study uncovered that the company had redundant solutions, inefficient requirement management, verification gaps, priority management gaps, and a lack of traceability. The overhead and productivity improvements in effort, collaboration, and tasks amounted to 1-3 months of time savings for teams across the organization’s resources. The investment in a system of systems and with refined processes was easily covered by the productivity improvement and the reduction in vendor solutions. Further, the new system brought native traceability across the segmented groups and silos and improved project oversight capabilities. The new system required fewer integrations, less maintenance, and fewer versions to manage by reducing total vendor software solutions by 32%.
As mentioned in the previous post, the critical finding that 50% of the time spent by the service team was actually wasted unnecessarily – due to inefficient systems and processes – demanded this immediate action and resolution.
But more about the Solution in our next blog post, where we will cover the answers in depth. Until then, if you are interested in learning more or doing a trial of Siemens lifecycle solutions, go here. And if you have questions, don’t hesitate to reach out.
Other Topics
This post is part of a broader safety series highlighting the challenges practitioners face during the development of safety critical ICs. To view other posts in the series, please refer to Guidelines to a successful ISO 26262 Lifecycle.