Study reveals targeted Digital Transformation initiatives offer significant benefits to manufacturing organizations
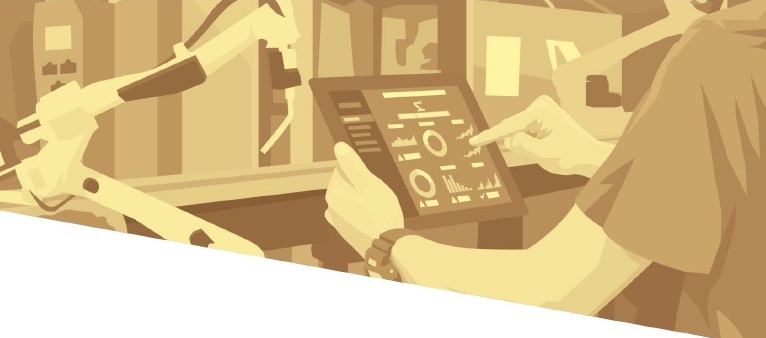
Digital transformation (DX) initiatives are gaining momentum among today’s leading manufacturers. Lifecycle Insights’ 2021 Return on Investment (ROI) of DX Study revealed that targeted DX initiatives offer significant benefits to manufacturing organizations. The study results, however, also highlight the vast differences between the least and most progressive organizations when it comes to reaching margin targets, reducing prototypes, and controlling inventory.
Lifecycle Insights’ 2022 Digital Twin Study
To better understand where, how, and when manufacturers were implementing DX efforts—and to see what progress companies had made since the previous study—Lifecycle Insights conducted the 2022 Digital Twin Study. This study surveyed respondents from the automotive, aerospace, electronics, industrial machinery, medical devices, energy, and consumer products sectors to gain new insight into how organizations were leveraging digital twins and digital threads. The study results revealed marked differences between the most progressive organizations and their least progressive peers in both product and production engineering. This post explores a few of the most interesting revelations about how companies are using digital twins and digital threads in product and production engineering.
Product and Production Digital Twins
Lifecycle Insights’ 2022 Digital Twin Study reveals exciting new details about the role of maturity when it comes to companies’ adoption of digital twins. To understand what that means, however, it is vital to define these terms.
A digital twin of a product consists of the definitions, documentation, and simulations that detail the form, fit, and function of every aspect of a particular product. Every system, every assembly, and every item are digitally represented. Most digital twins will include the product’s mechanical hardware, electrical distribution systems, electronics board systems, and even the embedded software. Engineers can use this comprehensive digital twin to develop and test the product, both in the digital realm and the physical one.
The production digital twin, on the other hand, encompasses everything required for manufacturing. Every operation, every cell, every line, and every system are represented—building up, when necessary, to the entire facility. Companies can create and manage manufacturing plans, models, test results, documents, robots, human simulations, and other related assets in a digital twin of their production environment. This model can then be used to optimize manufacturing tooling, numerical control (NC) machining, production lines, manufacturing facilities, and production floor data transfers.
It is also important to note, as part of their ongoing DX journey, many of the most progressive companies are also using advanced solutions like product data management (PDM), product lifecycle management (PLM), and application lifecycle management (ALM) to manage the increased number of digital artifacts associated with design and production. These solutions also influence the impact of DX initiatives. We will examine these factors, which are helping organizations gain the maturity they need to make the most of their manufacturing digital twins, below.
Managing Product Design Deliverables
Today’s products are becoming more and more complex. There is a rising demand for smart, connected products. These products will include not only mechanical hardware, but also electrical systems, electronics, and software. The interdependency of electrical and electronics systems with mechanical hardware creates another layer of complexity. Changes made to electrical or electronic board design impact mechanical hardware design. The reverse is also true. Managing the design of such complex products is not an easy task for engineering executives or design engineering teams. Many organizations have turned to advanced solutions like PDM, PLM, and ALM to help keep track of it all.
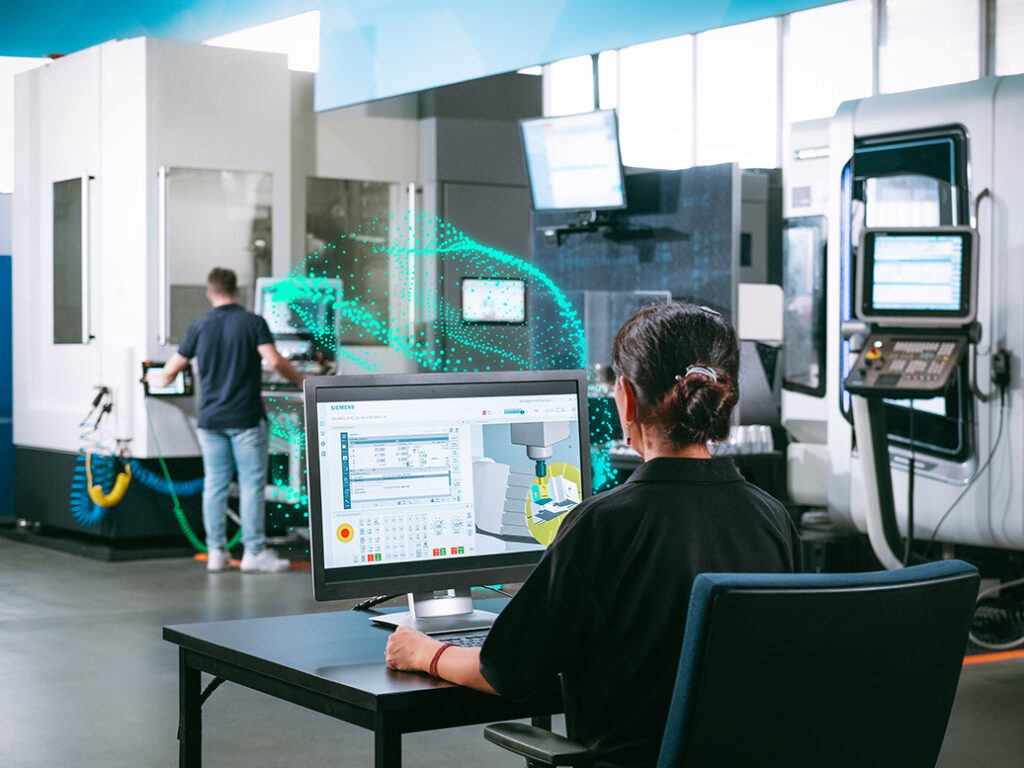
That said, we were surprised to find there is a big gap between the least progressive and most progressive organizations when it comes to leveraging these platforms, especially with mechanical design. Seventy-six percent of respondents from the most progressive companies reported using an advanced solution to manage their mechanical hardware designs. In contrast, virtually none of the companies in the least progressive category were using any of these advanced solutions in their own mechanical design processes. This gap between the two categories of companies is also apparent, if not as pronounced, in the design of electrical systems, electronics, software, and internet of things (IoT).
Failure to adopt advanced solutions means the least progressive organizations will fall behind their peers. They will have greater difficulty managing their product design costs and will take longer to get their products to market. And they will be more likely to find errors or other issues late in the product development lifecycle, resulting in delays and costly fixes.
As time goes by, two trends take over. The most progressive companies improve and find efficiency due to their long experience with PDM/PLM solutions. Also, the products that their customers demand from these manufacturing companies tend to be more complex. This means the gap will only expand.
Companies that adopt advanced solutions like PDM, PLM, and ALM will be able to better manage the design process and its associated deliverables. In doing so, they can catch up to their most progressive peers and realize tangible value across the entire product development lifecycle.
Managing Production Deliverables
Any great product starts with a great design. Yet, only a fool believes that design is the only area of engineering that affects a product’s ultimate success in the market. After all, good designs have to be manufactured. The most progressive organizations understand this, and leverage their DX initiatives in production engineering as well as in product design. The least progressive don’t, so once again, there is a wide discrepancy between the two when it comes to adopting advanced solutions like PDM and PLM to help manage production deliverables.
In discrete manufacturing, tooling and numerical control (NC) machining are essential elements of the production process. About 88% of the most progressive companies manage their tooling and NC machine codes using an advanced solution, but only 9-12% of the least progressive organizations reported the same. There was a similar but smaller gap when it came to using advanced solutions to manage digital representations and deliverables associated with manufacturing cells, production lines, and manufacturing facilities.
Managing production engineering deliverables is a challenging task. Using an advanced solution simplifies things by providing a single source of the truth in a central location. As a result, all stakeholders can rest assured they are working from the correct design deliverables.
When digital representations are available through an advanced solution, it is easier for manufacturing engineers to use them to select an optimized tooling strategy for production. They can use those deliverables to generate and test NC codes before moving to production, confident they are working with the most up-to-date models. By managing all these production-related activities using an advanced solution, the organization can ensure traceability and accountability throughout the manufacturing process.
When the least progressive organizations deploy an advanced solution to manage their product design and production deliverables, they can foster a seamless workflow between their design and manufacturing teams. Any changes on either the design or manufacturing side are effortlessly communicated to all stakeholders, enabling everyone to study the impact of any change and take the appropriate steps to support that change. The use of advanced solutions creates a process that is well documented and frictionless.
Conclusion
The manufacturing industry is seeing large gains from the adoption of various DX initiatives. Lifecycle Insights’ 2021 ROI of DX Study and 2022 Digital Twin Study demonstrate that the most progressive organizations are seeing many benefits from their adoption of digital twins and advanced solutions like PDM, PLM, and ALM to improve both product design and manufacturing processes. These benefits include better management of design deliverables, smoother design change processes, lower production costs, and fulfillment of margin targets. Companies who are not leveraging these DX initiatives should take note.
Read the full Digital Twin Study here.
Discover how companies are using digital transformation to turn complexity into a competitive advantage. Click here.