The digital twin’s changing role
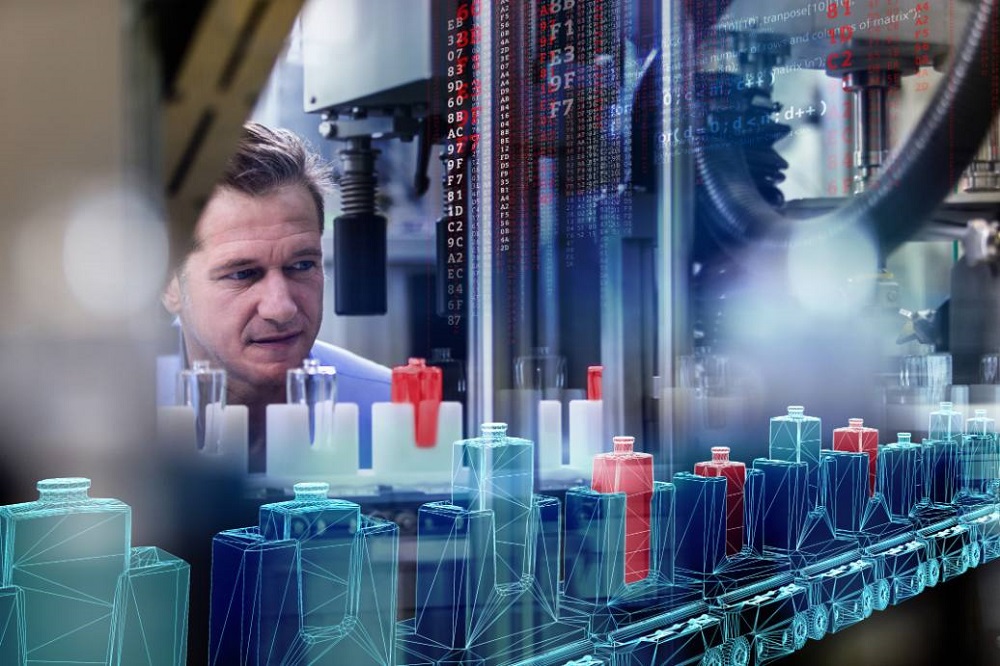
Over the past few years, the manufacturing industry has spent a lot of time discussing the value of the digital twin and the digital thread. Companies are learning that both are critically important to the success of digital transformation initiatives and their ability to improve product development, manufacturing, and service processes.
The value of the digital twin
Products of all shapes and sizes are becoming more and more complex. A comprehensive digital twin, or the complex virtual model of a particular physical product or system, helps manufacturers improve product design, troubleshoot issues, and make better decisions.
To make the most of a digital twin, the virtual representation should grow across development and manufacturing processes, dynamically expanding and reorganizing. As it evolves, various functional departments will use it in many ways across the product lifecycle.
Comprehensive digital twins provide value when used for both individual products as well as for more complex entities like manufacturing plants. What’s more, digital twins for products and plants are more interconnected than many may realize. Harnessed correctly, this link can help manufacturers improve, and even optimize, their products and processes by providing actionable design insights and strong operational efficiencies as the digital becomes physical.
The Product-Plant Lifecycle Connection
Any manufacturer will tell you a product and the plant that manufactures it have different lifecycles. Each of these two lifecycles progresses at its own pace, evolves differently, and relies on different kinds of definitions. Organizations may manufacture newly-designed products in previously-established plants or design new plants to support the needs of existing assembly components.
Yet, while the two lifecycles may start out as disconnected entities, they quickly become more intertwined as the initial, conceptual phases for each wind down. Your product influences your plant’s production process. Similarly, the capabilities of your plant can impact the ultimate product design. The relationship between product and plant, to borrow a phrase from biology, becomes symbiotic.
For example, a housing for a motor could be produced with varying tolerances. This decision not only affects the performance qualities and geometry of the component, but also places requirements on machining equipment in the manufacturing environment that must produce it. That decision may eliminate high-speed machining as an operation. It may prolong the time to complete the operation to inordinate levels. That, in turn, could slow down the production of the entire facility.
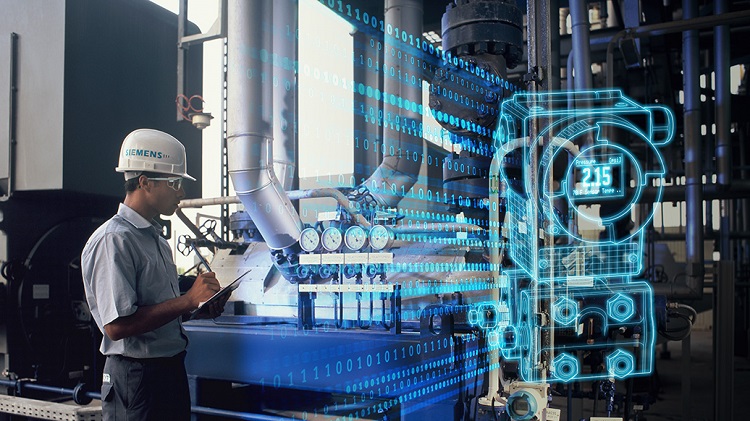
Likewise, the layout and equipment in a manufacturing environment could impact design decisions for that motor housing. A fast, powerful, piece of machining equipment at one end of the plant and a high-tolerance, finishing, piece of machining equipment at the other end of the plant could disrupt material flow in the plant. Perhaps the moderate-tolerance equipment that is much closer could be used instead.
As you can see, considering the impact of such decisions from the get-go is crucial to achieving a streamlined product development process and improved product outcomes. Decisions made for one without considering the other will lead to suboptimal performance and operation—and, over the long term, unnecessary costs.
Manufacturers that mine deep insights on both the product and plant sides can make more innovative products and realize significant production efficiencies as those products are being made.
Given the fact there is a many-to-many relationship between products and plants—that one product can be produced in many plants and one plant can produce a multitude of different products—it is critical that organizations proactively manage each in a holistic, integrated manner from the very beginning of the product development process. In this way, they can address potential gaps or issues that arise in the product-plant relationship in the virtual world before they become too costly in the physical world.
Digital Twins for the Product and the Plant
So how do these needs relate to the digital twin? You develop digital representations of both your product and plant so you can refine those designs, troubleshoot any issues, and connect different systems before building something physical. A comprehensive digital twin allows you to visualize the product and the plant virtually and identify and resolve any issues before actually creating something physical.
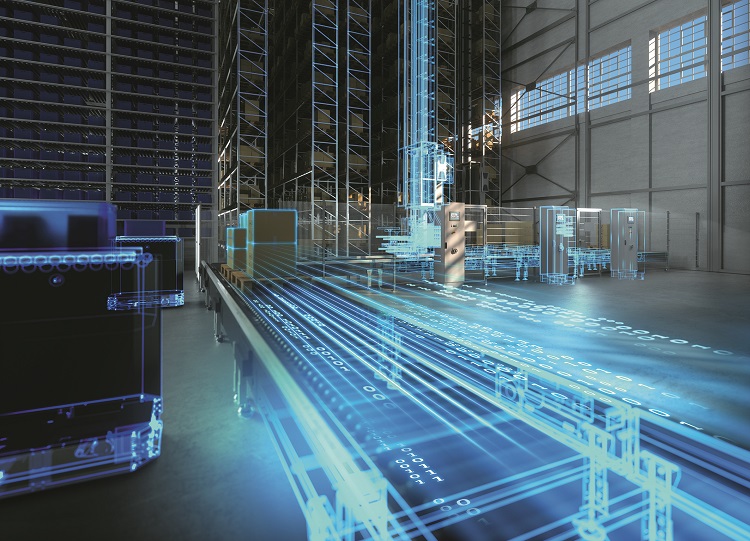
It is important to note that any new development lifecycle is almost completely digital at the start. You augment the digital representation with a physical instantiation over time. But the digital version never fades, because the virtual model is always there to mirror the operation of its physical aspects. A comprehensive digital twin remains through all the required steps of design, realization and operation. This is true for both products and plants.
The support the digital twin provides will vary depending on where you are in the product lifecycle. It plays different roles in different phases.
For example, during the design phase, the digital twin documents the definition and predicts performance. Once you move to realization, it guides the creation of physical instances. During the operational phase, the digital twin can help you improve performance by providing actionable, timely insights into how the different pieces of your product or plant are working. This sets you up to optimize various aspects of the manufacturing process.
There’s even more value to be gained when you look at the interaction between the comprehensive digital twins of your product and plant. Interconnected digital twins will allow everyone to understand the impact of a decision, either in the design of the product or in the manufacturing environment. In our example, maybe the design engineer and the production engineer realize that applying tight tolerances eliminates the option to use high-speed machining, resulting in longer manufacturing times. They can then make an informed decision about whether that is the right choice. This is dramatically different than making a blind decision, only to realize when production ramps up that the product takes longer to produce than anticipated.
Connecting the Digital Dots
Manufacturing organizations are increasingly looking to digital twins to save time and money in the product development lifecycle. These virtual models of both products and plants help organizations streamline the product development process from design to operation and leverage the symbiotic relationship between plants and products to gain insights that power more informed decisions. When organizations can create comprehensive digital representations of these related entities, they are in a better position to produce more innovative designs as well as avoid unnecessary costs or delays.
Additional links:
- Video: Where does a digital transformation start?
- Blog: Industrial digitalization during the pandemic and beyond
- Website: Xcelerator: Siemens’ comprehensive portfolio of software and services