Digital Threads and Business Processes
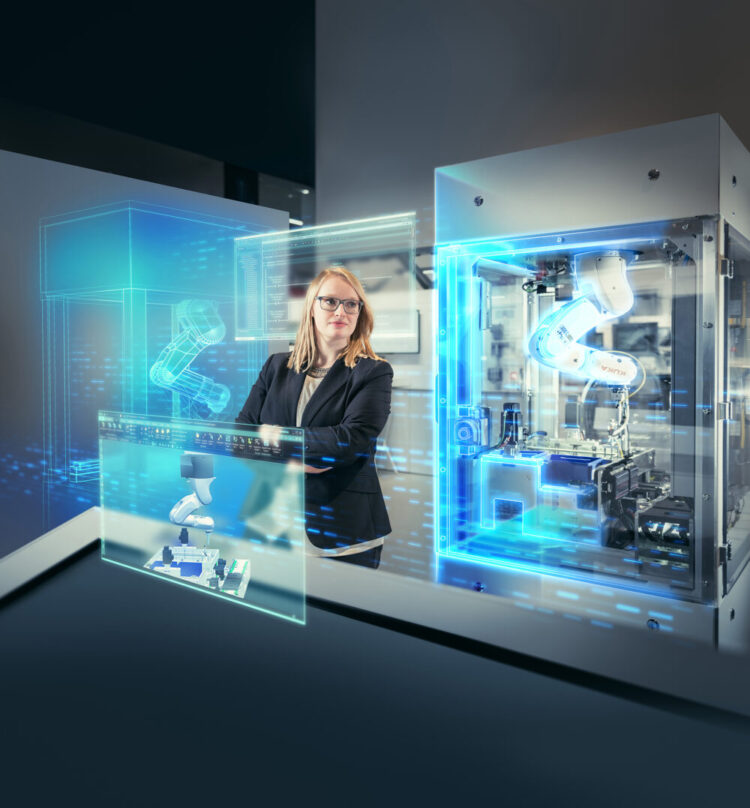
Manufacturers of all stripes are pursuing digital transformation efforts to meet the evolving needs of product development. The digital thread is a vital part of such initiatives. As manufacturers look for better ways to manage more complex products and processes through digital transformation, many are formalizing and improving their digital threads.
The Comprehensive Digital Twin, Explained
The digital twin of a product consists of the definitions, documentation, and simulations that detail the form, fit, and function of every aspect of a product: every system, every assembly, and every item in a product. The same holds true of the digital twin of a plant, except that it encompasses everything in manufacturing production, spanning every operation, every cell, every line or system, and even entire facilities. For more clarity, let’s review what comprises the digital twin at a more granular level. The digital twin consists of:
- system architectures, bills of materials (BOMs), and other things that represent the structure of the product or plant;
- 3D models, sketches, top-down-design space claims, concept models, schematics, diagrams, layouts, etc.; all of which are logical, functional, or physical representations of the product or plant;
- simulations and analyses, from one-dimensional ones all the way to complex 3D ones across many engineering physics and design domains such as structures, fluids, signal integrity, human operators executing a procedure in a cell, and much more;
- deliverables needed to execute operations or that describe intent, such as operator instructions, numerically controlled instructions such as toolpaths, design or configuration rules that drive sizing;
- requirements, specifications, standards, test cases and plans, and other text-based documentation that don’t necessarily have a one-to-one equivalent in the physical world but still describe the product; and
- data coming from simulations, physical tests, or even post-delivery product and production operation.
Overall, it is key to recognize that the digital twin is a composite representation. No single definition, documentation, or simulation alone describes even a fraction of the whole product. It is only when these aspects are understood collectively that an organization can grasp the form, fit, and function of the product or the plant.
Digital Threads, Explained
A digital thread is a discrete, linked, traceable sequence of activities in the product or production lifecycle, that is digitized and automated.
Digital threads range widely in scope and provide means to navigate fast and flexibly through all systems of record. Some are executed completely in engineering. Others run only in manufacturing. Yet others span both engineering and manufacturing. Likewise, some focus exclusively on the product. Others on the plant. Some span both. And still others connect products in operation/service with key areas of product development.
Examples of digital threads include:
- the system engineering flow that defines requirements or specifications and breaks them down into sub-requirements, builds out functional architectures, creates physical architectures, and connects all of them together;
- planning and designing a production facility where engineers shift manufacturing lines and systems while simulating material flow;
- the prototype and test process where engineers assemble and integrate the first, physical version of a product to run hybrid physical-digital test cases; or
- the virtual commissioning sequence where engineers digitally validate the logic of manufacturing equipment controllers for production processes.
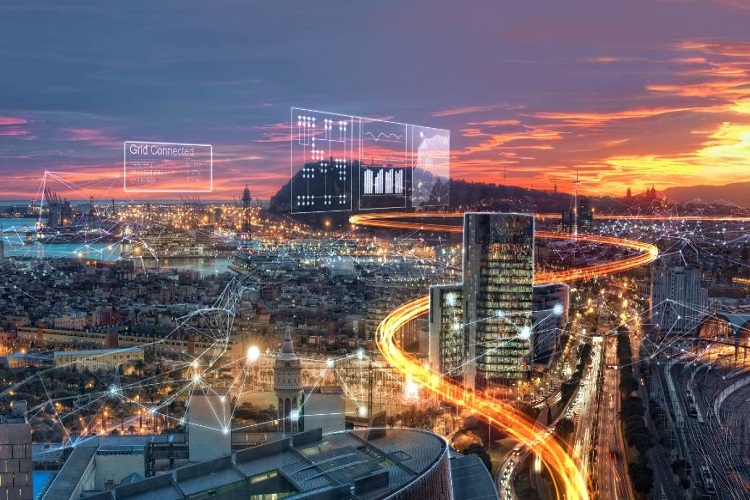
Digital Threads Build a Comprehensive Digital Twin
Digital threads and the comprehensive digital twin directly affect one another. Individual digital threads—or a series of digital threads—expand comprehensive digital twins over time.
- Initially, at the start of development, the digital twin starts as nothing. Product ideas and production concepts exist only in people’s thoughts.
- After the start of development, initial aspects of the digital twin are defined. This most often starts as requirements, but quickly turns to concepts, architectures, and system definitions such as functions, logic definitions, and more.
- Once detailed design hits, each design domain builds out in-depth digital definitions, documentation, and simulations specific to that engineering discipline. This results in an explosion of digital content including diagrams, models, simulations, drawings, and so much more.
- The comprehensive digital twin has two intersecting lifecycles: product and production. The product is the asset that is being created and the production is how it will be produced.
- The digital twin of the product and the digital twin of production intersect. They influence and impact each other over time.
- When production starts, digital definitions and documentation are used to make the physical instantiation of the product or plant. The virtual and real worlds now merge to create a digital twin.
- Once delivered, the physical product, plant, system, line, cell, or piece of equipment can stream data back to its virtual sibling, the digital twin, so that the digital twin can mimic or even predict real-world behavior. These simulations enable real-time product and production optimization via continuous closed-loop feedback from the physical world.
Of course, the reality of development is far more nuanced. Few development efforts for a new product or plant start completely from scratch. Almost all new products or plants reuse entire systems, operations, assemblies, and many components completely, or at least as a starting point. This means that some digital threads integrate existing things into the product or plant while other digital threads are leveraged to develop brand new things.
Digital Transformation Initiatives
Today, many engineering and manufacturing leaders know they need to improve how they develop products and plants. A sea change towards smart, connected features in both has outstripped traditional development approaches.
Such improvement efforts have, in general, fallen under the newly coined term, digital transformation. This class of initiatives relies heavily on digital methods to realize performance improvements, especially in the most challenging areas of product and plant development. Digital transformation efforts commonly fall into one of several categories:
- One class of digital transformation initiatives focuses on switching from disparate, siloed representations of products and plants to more a comprehensive digital twin.
- Another class of digital transformation initiative focuses on shifting manual activities and whole processes that rely on hardcopy or simple electronic artifacts to more digital, automated digital threads.
- Often, companies pursue some combination of instilling comprehensive digital twin and digital threads as part of a single improvement effort.
Overall, companies seek such changes to improve organizational performance, relying on improved collaboration around a shared source of the truth, better prediction of performance and operation, more clarity and better access to documentation, and much more.
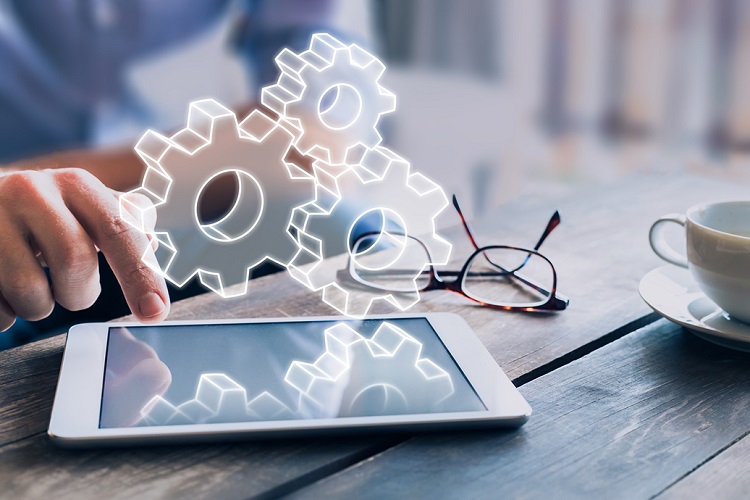
Digital Threads are Industry- and Company-Specific
While every company relies on many digital threads in its development process, each will have variants. Some are standard for an industry. Others are unique to a company.
Some industry-specific digital threads are enforced by third parties. These include regulatory compliance or standards-enforcement processes for which there is no variation from company to company. Each organization must comply. For example, the Food and Drug Administration (FDA) has regulatory-driven procedures around the lab documentation for drug development. Another example is the standard verification, validation, and certification of flight control software for the aviation and aerospace industry.
Other industry-specific digital threads are common practices and approaches that are generally accepted in that industry. Companies can choose not to leverage these digital threads. However, it is in their best interest to use some version of them. For example, it’s necessary in the automotive industry to use a systems-driven method to develop electrical and electronic (E/E) systems.
Yet other digital threads are company-specific. Sometimes, these digital threads are significant differentiators, offering a competitive advantage. Others represent a unique way of executing a process that does not offer differentiation, yet is now the standard way of executing activities internally. Those particular digital threads have become the norm, and changing them would be disruptive.
Recognizing this reality is important as different companies consider and build out their own digital transformation initiatives.
Conclusion
As more manufacturing organizations look to make targeted improvements across the product and factory lifecycle, they see the value in pursuing digital transformation efforts. Such efforts can help enhance both product development and production activities from the very start of those lifecycles.
Yet, to find greater success in these initiatives, organizations should consciously plan out their digital thread and digital twin strategies, as a map for their digital transformation initiatives. The digital thread significantly enhances the comprehensive digital twin by providing integral data and context that can inform every phase of the product lifecycle or production timeline. And, as different industries and organizations are putting their own unique spin on the digital thread, small differences can quickly become competitive differentiators.