What is the comprehensive digital twin?
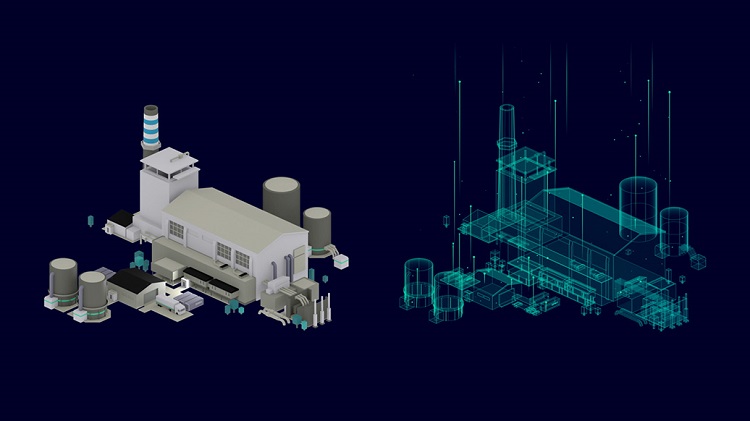
Companies in all industries face a future of tougher competition, and exacting and personalizing product requirements, while dealing with yesterday’s development processes. Your competitors are constantly developing new products, features or services as the cycle of innovation shrinks. Add to that, new environmental regulations calling for the reduction of carbon emissions to meet global climate goals, much sooner rather than later.
Meanwhile, there is an explosion of complexity in product development, manufacturing processes, and data capture and analysis. No industry is exempt from complexity, whether building tomorrow’s autonomous vehicle, producing today’s smart watches or using sophisticated industrial machinery to supply various OEMs. Connecting data sensors and AI robots on the factory floor are semiconductors and embedded systems integrated into multiple complex subsystems and components from hardware, electrical, electronic, and software domains.
This is why digital transformation adoption is more critical now than ever before. As complexity continues to grow, it will go beyond a competitive advantage to become a competitive necessity.
At Siemens, we believe there are three imperatives to implementing a successful digital transformation:
- A comprehensive digital twin enables customers to create closed-loop connections between the virtual and physical worlds across the entire value chain, thereby developing actionable insights and informed decisions
- Adaptable, open, and flexible solutions that quickly adapt to changing business conditions provide a competitive advantage for customers to outpace their competition, including improved product quality, cost savings and faster time to market
- The ability to leverage a vast and robust ecosystem of partners and developers that build, sell, support, deploy, implement and service solutions that enhance productivity, efficiency, cost savings and measurable business outcomes
This blog will touch on the comprehensive digital twin and explain its benefits and how it helps turn complexity into your competitive advantage.
The comprehensive digital twin
Digital transformation uses resources efficiently and creates a more sustainable industry. At its core is the comprehensive digital twin, which combines the real and the digital worlds, makes it possible to seamlessly integrate the entire value chain from design to realization, while optimizing via continuous flow of data.
Working with a comprehensive digital twin makes it possible to integrate the entire product lifecycle – and if required – even the factory and plant lifecycle. The generated performance data captured in the physical world enables a continuous and open loop of optimization for both the product and the production. This comprehensive digital twin approach integrates all necessary components, including the building, which can be used to optimize the performance and efficiency of a plant’s energy and physical infrastructure.
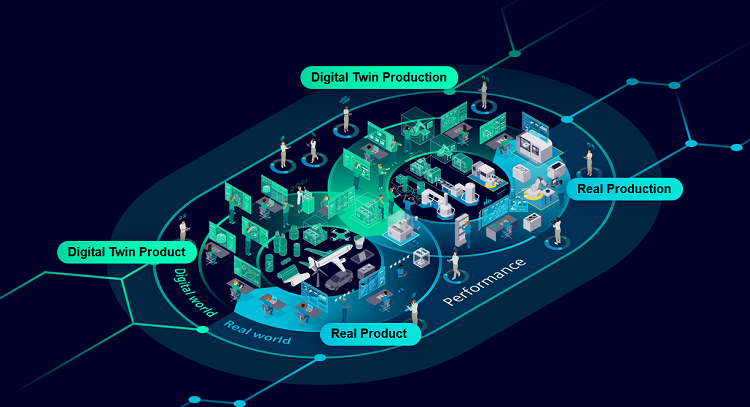
The comprehensive digital twin brings together processes that were previously separate. It breaks down traditional silos and helps bridge the gaps between software and hardware, IT and OT, shop floor and top floor. By working cohesively in this environment, teams can work on the same iterations, at the same time, ensuring faster and more efficient design and decision-making.
Overall, the comprehensive digital twin is a virtual representation of a physical object that evolves and changes over time along with the product it represents. It merges the virtual and real world, blurring the boundaries between engineering and process domains.
Many organizations are benefiting from leveraging a comprehensive digital twin. Tomorrow’s electric and autonomous vehicle makers are using it. Legacy aircraft manufacturers are flying digitally before building, reducing prototypes and minimizing costs and resources.
The comprehensive digital twin isn’t just for large enterprises. There are startups and small businesses embracing the comprehensive digital twin as a means to better compete, reduce time-to-market and work with greater efficiency. Look no further than UK-based TrakRap, which creates specially engineered 100% recyclable film and pack designs. The comprehensive digital twin has helped them reduce plastic use by 70 percent, energy consumption by 90 percent and development costs by 30 percent. So it’s good for your wallet – and the environment!
Read TrakRap’s story of success here.
The benefits of the comprehensive digital twin
The comprehensive digital twin is just that: comprehensive. This single digital twin is not only a virtual representation of a product, but also includes and supports the numerous lifecycle phases and respective models of actual product behavior. It’s the foundation for flexible and efficient manufacturing and provides realistic simulation and validation of products, machines, lines and complete plants.
With a comprehensive digital twin, companies are finding fewer prototypes, fewer tests, and less waste during production, empowering engineering teams to design, build and optimize next-generation products faster and cheaper.
The comprehensive digital twin:
- Offers a precise virtual representation of the product or process flow that matches the exact physical form, functions and behavior of the product and its configurations
- Participates across the product and process lifecycle to simulate, predict, and optimize the product and production system used to create the product
- Connects real-world operational data back into product design and production over the lifetime of the product to continuously improve quality, efficiency, and quickly respond to customer demands or market conditions
The comprehensive digital twin means more than just product innovation. It provides the structure to transform your company into a digital enterprise from process innovation to modernizing core business models. As companies digitalize processes or data flows, they will start to weave digital threads.
When digital twin combines these digital threads it adds monumental value to the collaborative development of the product across the different teams—mechanical, electronic, electrical, software and manufacturing—enabling numerous data processes across multiple systems. Merging the physical and digital worlds with a digital thread enables users to predict performance and optimize their product.