3 things to know about IT/OT convergence (including what it is and why it matters)
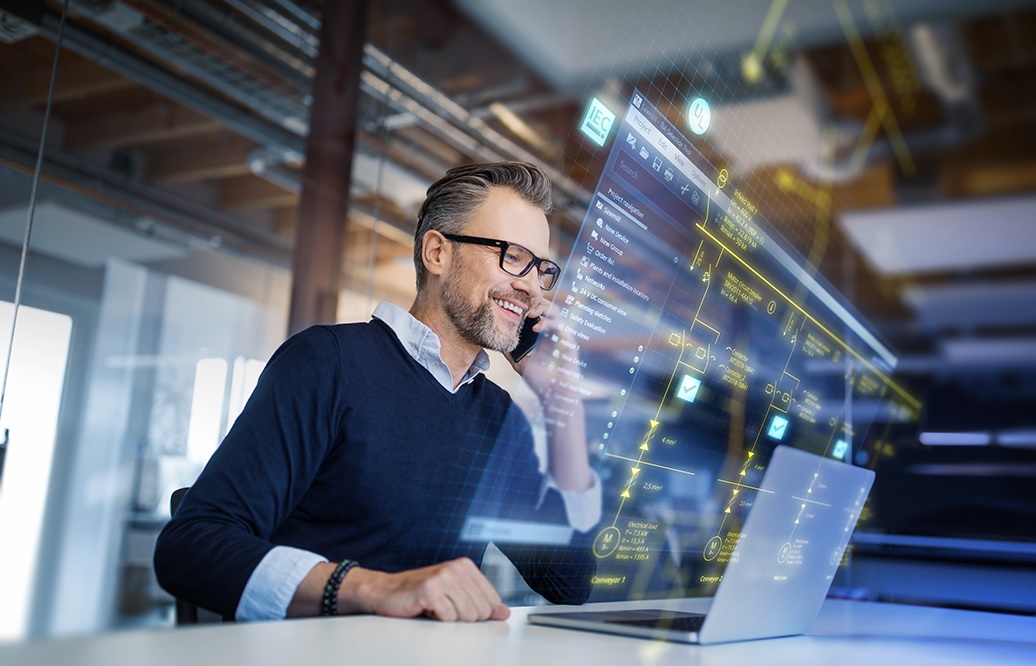
Not only are products increasing in their complexity, but so are the methods in which they are manufactured. It’s no wonder that manufacturers are searching for innovative ways to tackle a multitude of challenges, which include everything from increased product complexity and sustainability goals to demands for more personalized and customized products.
To manage the overwhelming and seemingly nonstop challenges, manufacturers are looking toward the digital future to achieve a higher level of smart manufacturing.
Once upon a time, automation was considered a means for reducing costs. However, digitalization delivers more, better data while optimizing cost. Manufacturers can use this data to maximize factory utilization and real-time management of supply chains, and improve time to market, to name a few examples.
There are three key capabilities to know when it comes to how digitalization supports, and leads to, smart manufacturing:
- The convergence of information technology (IT) with operational technology (OT)
- Closed-loop manufacturing and execution designed to optimize the actual process of production
- Closed-loop quality which ensures the accurate delivery of products the first time.
The good news is that the digital technology to create a smart manufacturing environment is available today. The convergence of IT with OT data delivers a wealth of data that can be used to continuously improve operational efficiencies within a closed-loop manufacturing environment.
The agile and adaptable approach to the smart manufacturing process means optimizing throughput while lowering costs and improving sustainability by minimizing resource usage, electricity, and waste, to name a few.
Let’s go more in-depth to the three capabilities.
1. What is IT/OT convergence?
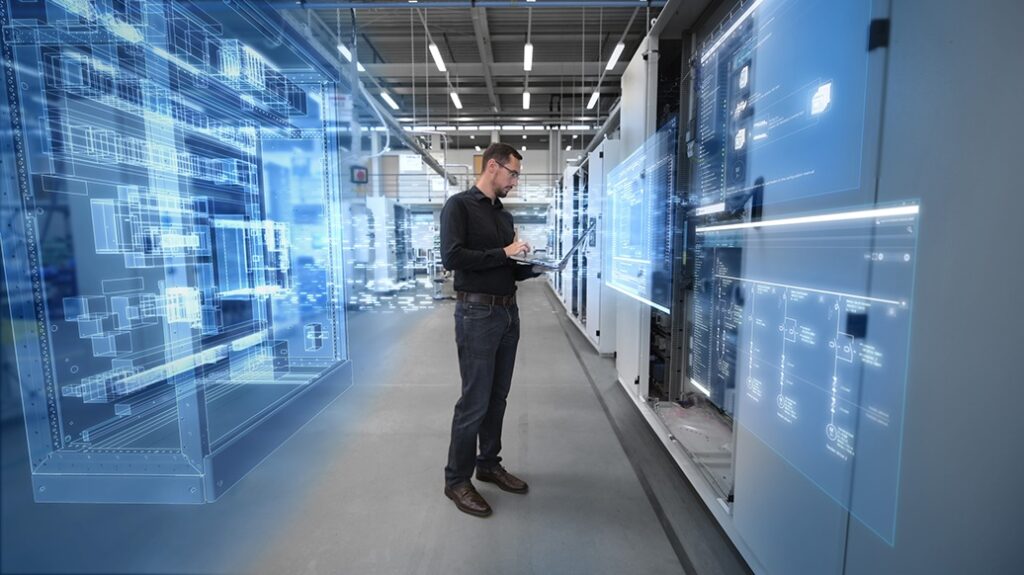
OT is the software that governs the operation of the physical equipment, the controls and the technology. The software ensures the hardware executes the instructions it’s supposed to.
IT is the company’s computer technology. It stores, retrieves, processes, analyzes and recommends action based on digital data extracted from operations.
Management uses IT to make decisions and factories use OT to drive actions.
The challenge is how to get the most accurate, comprehensive data for factory operations. Most factories are a mix of older and newer equipment. The newer smart machines are designed to share data, but older machines are data islands. Therefore, a network of sensors are added to connect those islands to ensure data across all manufacturing operations are brought together for analysis.
This is IT/OT convergence.
And this matters because real-time process monitoring of the shop floor enables managers to quickly assess the business impact of manufacturing activity and allows for greater flexibility and visibility into operations while empowering manufacturers to make better decisions for the machines and production.
IT/ OT convergence is the initial crucial step to achieving smart manufacturing.
2. Optimizing operations with closed-loop manufacturing
IT/OT convergence promotes closed-loop manufacturing allowing manufacturers to synchronize and optimize production across product design, production planning, manufacturing execution, automation and even intelligence from consumer use in the field.
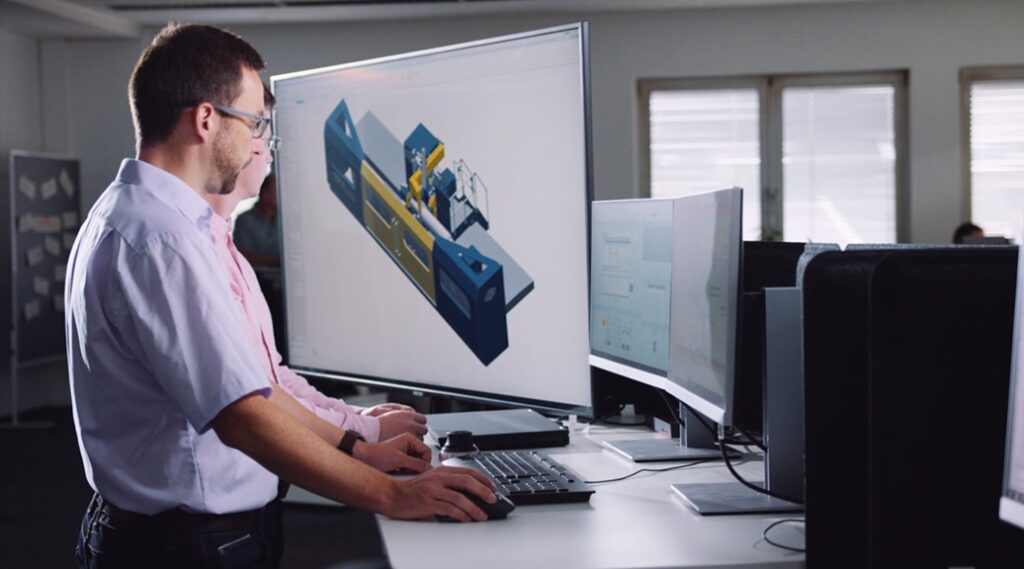
This connected loop of information helps them continuously improve the cost, time and quality of the manufacturing process and lead to faster product innovation and delivery.
What closed-loop manufacturing does is ensures that all teams have real-time information at each step in the manufacturing process. Manufacturing operations management, or MOM as it is often referenced by, enables manufacturers to collect and maintain a wealth of data on the production and the physical products being produced.
Accessing this data means engineering teams are receiving feedback that helps resolve problems and track what has been built with all the data, how it was built, and with what materials and parts.
With IT/OT convergence and closed-loop manufacturing, when a machine goes down, the manufacturer can assess the problem and determine its impact on production. Changes can be implemented quickly with minimal delays.
3. Delivering closed-loop quality
Quality is when the product outcome meets the intended expectations for product performance and features. Each and every product should meet this expectation. With closed-loop manufacturing in place, the manufacturer can not only identify and correct any issues but can also adjust the processes in real time to improve the quality of the product while minimizing scrap and rework. Early identification translates to reduced costs and better products.
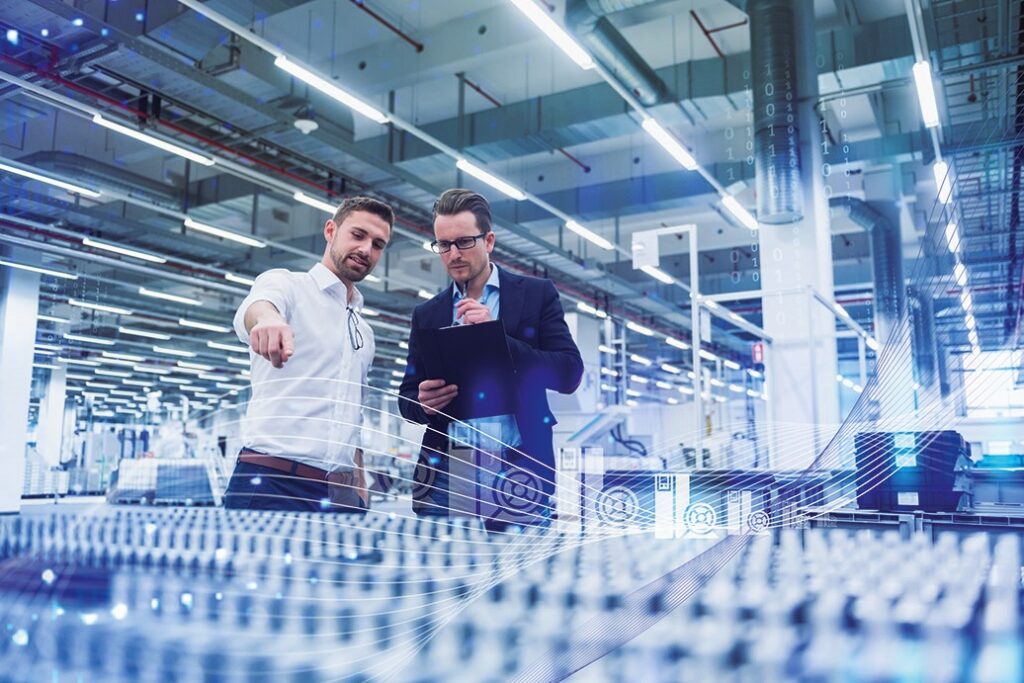
Closed-loop quality ensures products and parts are delivered correct the first time through optimization while providing the next level detail in terms of digitalization. It can also be used to improve the product over time. But to deliver on quality, it’s crucial to identify and correct subpar results early on. This includes developing expectations and capabilities, expected failure modes and the corresponding procedures for addressing those issues, and even looking at environmental and machinery conditions.
Organizations that establish a closed-loop quality process can achieve a median product compliance rate of 99 percent. What does it mean if the compliance rate drops below that? The lower percentage impacts performance and it could mean losing market introductions to the competition, expensive product recalls or failure to win future contracts. The key advantage of closed-loop quality is it shifts quality from a disconnected or isolated process to a shared responsibility.
Achieving smart manufacturing and IT/OT convergence with the comprehensive digital twin
For manufacturers looking to stay competitive in the future, smart manufacturing supports the concept of a digital twin of the manufacturing environment.
Within the factory, the digital twin provides a virtual, digital replica (hence, twin) of everything including a machine, manufacturing system or shop floor all within in a digital environment. More data feeds the digital twin so it can continuously combine the virtual and physical worlds and provide new insights and efficiencies for product manufacturing. And it is the IT/OT convergence that delivers the real-time data and information needed to create this comprehensive digital version of the factory. The more data there is, the better the comprehensive digital version of the factory, which is the basis for improving the real-world version via simulation of the digital model, thus closing the loop for manufacturing operations and quality.
Building the factory of tomorrow
Companies of all sizes are discovering that the more investment they make into digitalization, the better prepared they are for the future. Analysts have found that the most important aspect of digital transformation is to start or continue based on the needs of the company – therefore, every journey will be different.

It all starts with IT/OT convergence. The fusion of IT with OT data to tap into a wealth of data for continuously improving operational efficiencies within a closed-loop manufacturing environment. That, in turn, enables a closed-loop quality approach to constantly enhance product quality.
With the Siemens Xcelerator Software for Industry, manufacturers are finding the tools they need to allow all their resources, from talent to machines to products, to collaborate and benefit from their data sets. The depth and breadth of the portfolio ensures manufacturers have the best tools to collect and analyze data, use that information to make better, faster decisions and ensure an overall higher quality of their process and product.
Learn more about Siemens Xcelerator Software for Industry here.
Want to learn more about IT/OT convergence. Click here to listen to our podcast.